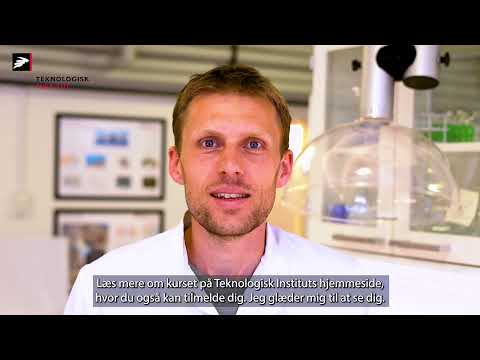
Indhold
- Baggrund for naturligt gummi
- Fremstilling af naturgummi
- Oprettelse af syntetisk gummi
- Forarbejdning af gummi
I slutningen af 1930'erne brugte De Forenede Stater over halvdelen af verdens forsyning med naturgummi. I dag kan naturgummi findes i over 50.000 fremstillede produkter i USA, og USA importerer over 3 milliarder pund naturgummi hvert år. Over 70 procent af gummi, der bruges i moderne fremstillingsprocesser, er imidlertid syntetisk gummi.
Baggrund for naturligt gummi
Naturgummi begynder som latex. Latex består af polymeren kaldet polyisopren suspenderet i vand. Langkædede molekyler sammensat af mange (poly) individuelle enheder (mers) forbundet sammen danner polymerer. Gummi er en speciel form for polymer kaldet en elastomer, hvilket betyder, at polymermolekylerne strækker sig og bøjes.
Mere end 2.500 planter producerer latex, et mælke-lignende sap-type materiale. Mælkevæg er måske den mest kendte latexproducerende plante for mange mennesker, men kommerciel latex kommer fra et enkelt tropisk træ, Hevea brasiliensis. Som navnet antyder, stammede gummitræet i det tropiske Sydamerika. For over 3.000 år siden blandede mesoamerikanske civilisationer latex med morgenherlighedsaft for at skabe gummi. Ændring af forholdet mellem latex og morgenherlighedsaft ændrede gummiets egenskaber. Fra hoppekugler til gummisandaler kendte mesoamerikanerne og brugte gummi.
Før 1900 kom mest naturgummi fra vilde træer i Brasilien. Da det 20. århundrede begyndte, overførte udbud og efterspørgsel produktionen med den stigende popularitet af cykler og biler. Frø, der blev smuglet ud af Brasilien, førte til plantager af gummitræer i det sydøstlige Asien. I 1930'erne varierede anvendelser med naturgummi fra dæk på køretøjer og fly til de 32 pund, der blev fundet i en soldats fodtøj, tøj og udstyr. På det tidspunkt kom størstedelen af den amerikanske gummiforsyning fra Sydøstasien, men 2. verdenskrig afbrød USA fra størstedelen af dens forsyning.
Fremstilling af naturgummi
Fremstillingsprocessen af naturgummi begynder med høst af latex fra gummitræer. Høsting af latex fra gummitræer starter med at score eller skære ned i træets bark. Latex strømmer ind i en kop bundet til bunden af udskæringen i træet. Latexmaterialet fra mange træer akkumuleres i store tanke.
Den mest almindelige metode til ekstraktion af gummiet fra latex bruger koagulering, en proces, der klemmer eller fortykner polyisopren i en masse. Denne proces gennemføres ved tilsætning af en syre, såsom myresyre, til latexen. Koagulationsprocessen tager ca. 12 timer.
Vand presses ud af koagulummet af gummi ved hjælp af en række ruller. De resulterende tynde lag, ca. 1/8 tomme tykke, tørres over trækrakke i røghuse. Tørringsprocessen kræver generelt flere dage. Den resulterende mørkebrune gummi, nu kaldet ribbestemt røgplade, foldes i baller til levering til processoren.
Ikke alt gummi ryges dog. Gummitørret ved hjælp af varm luft i stedet for at ryge kaldes et lufttørret ark. Denne proces resulterer i en bedre kvalitet af gummi. En endnu større kvalitet gummi kaldet bleg crepe gummi kræver to koagulationstrin efterfulgt af lufttørring.
Oprettelse af syntetisk gummi
Flere forskellige typer syntetisk gummi er blevet udviklet gennem årene. Alt resultat fra polymerisation (linking) af molekyler. En proces kaldet additionspolymerisation strenger molekyler sammen i lange kæder. En anden proces, kaldet kondensationspolymerisation, eliminerer en del af molekylet, når molekyler er bundet sammen. Eksempler på additionspolymerer inkluderer syntetiske gummier fremstillet af polychloropren (neoprengummi), et olie- og benzinresistent gummi og styrenbutadiengummi (SBR), der anvendes til ikke-hoppegummi i dæk.
Den første seriøse søgning efter syntetisk gummi begyndte i Tyskland under 1. verdenskrig. Britiske blokader forhindrede Tyskland i at modtage naturgummi. Tyske kemikere udviklede en polymer fra 3-methylisopren (2,3-dimethyl-1,3-butadien) enheder, fra acetone. Selv om denne erstatning, methylgummi, var ringere end naturgummi, producerede Tyskland 15 ton pr. Måned ved udgangen af WWI.
Fortsat forskning førte til syntetiske gummier af bedre kvalitet. Den mest almindelige type syntetisk gummi, der i øjeblikket er i brug, Buna S (styrenbutadiengummi eller SBR), blev udviklet i 1929 af det tyske firma I.G. Farben. I 1955 udviklede den amerikanske kemiker Samuel Emmett Horne, Jr. en polymer på 98 procent cis-1,4-polyisopren, der opfører sig som naturgummi. Dette stof kombineret med SBR er blevet brugt til dæk siden 1961.
Forarbejdning af gummi
Gummi, hvad enten det er naturligt eller syntetisk, ankommer til processorplanter (fabrikator) i store baller. Når gummien ankommer til fabrikken, gennemgår forarbejdningen fire trin: blanding, blanding, formning og vulkanisering. Formuleringen og metoden til gummiblanding afhænger af det tilsigtede resultat af gummiproduktionsprocessen.
Sammenblandingen
Forbindelse tilføjer kemikalier og andre additiver til at tilpasse gummien til det tilsigtede brug. Naturgummi ændrer sig med temperaturen og bliver sprød af kulde og et klæbrigt, sløret rod med varme. Kemikalier tilsat under blanding reagerer med gummiet under vulkaniseringsprocessen for at stabilisere gummipolymererne. Yderligere additiver kan indbefatte forstærkende fyldstoffer til forbedring af gummiets egenskaber eller ikke-forstærkende fyldstoffer til forlængelse af gummiet, hvilket reducerer omkostningerne. Den anvendte fyldstof afhænger af det endelige produkt.
Det mest almindeligt anvendte forstærkende fyldstof er kønrøg, afledt af sod. Carbon black øger gummiets trækstyrke og modstand mod slid og rivning. Carbon black forbedrer også gummiernes modstand mod ultraviolet nedbrydning. De fleste gummiprodukter er sorte på grund af kuldrøde fyldstof.
Afhængig af den planlagte anvendelse af gummiet, kan andre anvendte additiver omfatte vandfrie aluminiumsilicater som forstærkende fyldstoffer, andre polymerer, genanvendt gummi (normalt mindre end 10 procent), træthedreducerende forbindelser, antioxidanter, ozonbestandige kemikalier, farvestoffer, plastificeringsmidler , blødgørende olier og form-frigivende forbindelser.
blanding
Tilsætningsstoffer skal blandes grundigt ind i gummien. Den høje viskositet (modstand mod strømning) af gummien gør blandingen vanskelig at opnå uden at hæve gummitemperaturen høj nok (op til 300 grader Fahrenheit) til at forårsage vulkanisering. For at forhindre for tidlig vulkanisering foregår blandingen normalt i to trin. I den første fase blandes additiver som kønrøg i gummien. Denne blanding omtales som en masterbatch. Når gummien er afkølet, tilsættes kemikalierne til vulkanisering og blandes i gummien.
Shaping
Formning af gummiprodukter forekommer ved anvendelse af fire generelle teknikker: ekstrudering, kalandering, belægning eller støbning og støbning. Mere end en formningsteknik kan anvendes, afhængigt af det endelige produkt.
Ekstrudering består af at tvinge meget plastisk gummi gennem en række skrueekstrudere. Kalandrering passerer gummiet gennem en række stadig mindre mellemrum mellem ruller. Rulle-dyse-processen kombinerer ekstrudering og kalandrering og producerer et bedre produkt end hver enkelt individuel proces.
Belægning bruger kalandreringsprocessen til at påføre et lag gummi eller til at tvinge gummi ind i stof eller andet materiale. Dæk, vandtætte kludetelt og regnfrakker, transportbånd samt oppustelige flåder fremstilles ved at belægge materialer med gummi.
Gummiprodukter som skosåler og hæle, pakninger, tætninger, sugekopper og flaskestop støbes ved hjælp af forme. Støbning er også et trin i fremstilling af dæk. De tre primære metoder til støbning af gummi er kompressionsstøbning (anvendes til fremstilling af dæk blandt andre produkter), transferformning og sprøjtestøbning. Vulkanisering af gummiet finder sted under støbningsprocessen snarere end som et separat trin.
vulkanisering
Vulkanisering afslutter gummiproduktionsprocessen. Vulkanisering skaber tværforbindelser mellem polymererne i gummi, og processen varierer afhængigt af kravene til det endelige gummiprodukt. Færre tværforbindelser mellem gummipolymererne skaber en blødere, mere bøjelig gummi. Forøgelse af antallet af tværforbindelser reducerer gummiets elasticitet, hvilket resulterer i hårdere gummi. Uden vulkanisering ville gummi forblive klistret, når det er varmt og sprødt, når det er koldt, og det ville rotere meget hurtigere.
Vulkanisering, oprindeligt opdaget i 1839 af Charles Goodyear, krævede tilsætning af svovl til gummi og opvarmning af blandingen til 280 F i cirka fem timer. Moderne vulkanisering bruger generelt mindre mængder svovl kombineret med andre kemikalier til at reducere opvarmningstiden til 15 til 20 minutter. Der er udviklet alternative vulkaniseringsteknikker, der ikke bruger svovl.